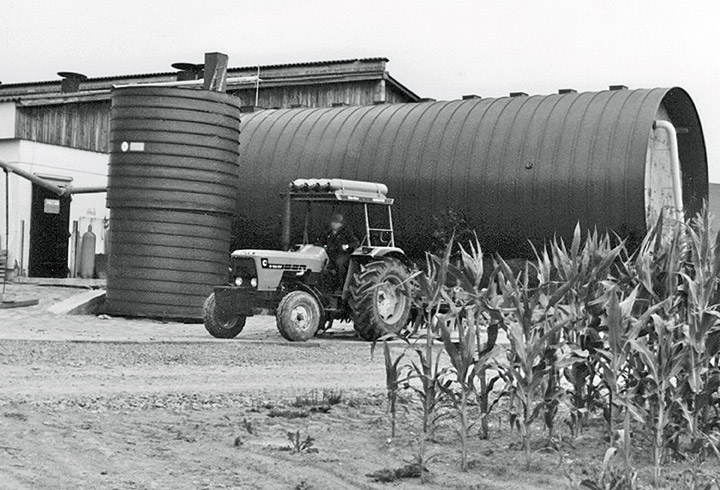
LIPP® Digester
Development of the first Digesters since 1971
LIPP began speculating about alternative energy sources as early as 1971. As a response to the oil crisis at that point, the company began tests on the family farm, where the silos were being used for the first time as reactor tanks. With support from the universities of Weihenstephan and Hohenheim, he succeeded in creating energy from organic materials.
Four digester types for different applications
In the 1970s, a digester with a horizontal fermentation process was created, with a paddle agitator and a screw conveyor. At the end of the 1980s, biogas plants were beginning to gain popularity as alternative sources of energy. Lipp customers were able to benefit from the know-how gained over the previous years of development. Further development and optimisation of the digester led to the creation of four different digester types, each suitable for a different application.
Modular KomBio® Reactor with integral gas accumulator
More than 50 years experience in digester development ensures that our patented KomBio® Reactors are the ideal complete solution, right down to the finest detail. This high-quality, universal digester is ideal for both industrial and municipal applications. It has also been used in hundreds of agricultural applications. The reactor combines a state of the art industrial gas accumulator with a high performance digester giving optimum mixing and thermal yield.
The individual components of the tank benefit from numerous innovations. First of all, the integral gas accumulator offers many advantages, for example sealed integration of the flexible gas accumulator membrane in a surge tank, which reduces gas losses. The fixed roof construction, which can be insulated, ensures protection of the gas accumulator membrane from the effects of weather and therefore extends the life of the membrane considerably. In addition, the heating for the KomBio® Reactor is outside the stainless steel container (Verinox®), ensuring good heat input for the entire filled height of the tank. Up to 200 mm of insulation enables the unit to be used both in cold and hot regions across the world. An additional feature of the KomBio® Reactor is the patented agitator technology, which makes the digester suitable for a wide variety of substrates and ensures uniform container mixing.
All digester components are designed and selected individually for the requirements of the fermentation process. The Lipp System on-site construction method enables construction anywhere in the world with the same levels of quality. The package is completed by modular extension options.
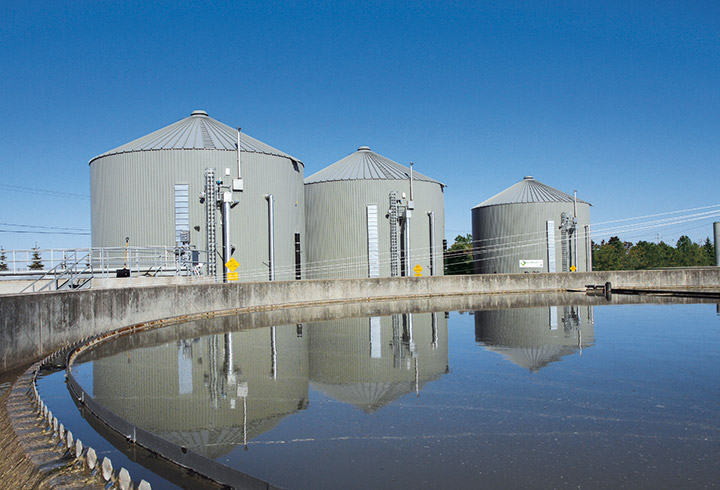
Universal Digester with optimum diameter – height ratio and high quality stainless steel diaphragm roof
The Universal Digester is an additional development for large industrial and municipal plants. Maximum life is the central focus for this container, with a stainless steel tank (Verinox) combined with a welded stainless steel diaphragm roof ensuring the highest quality for the inner part of the container. As a post-digester, a digester is also an ideal solution for farming applications.
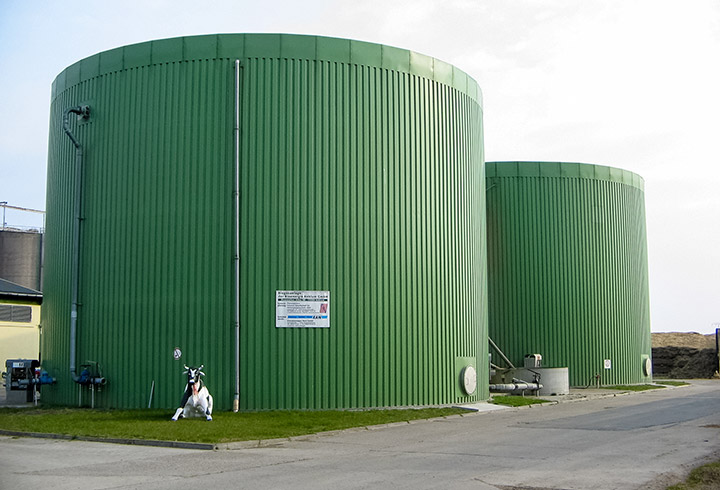
The Universal Digester, just like the KomBio® Digester enjoys the advantages of external heating, which, thanks to the good thermal conductivity of the steel, ensures uniform heating over the entire filled height of the tank. Good insulation of the container wall and roof construction minimises heat losses from the fermentation process. Flexible agitation‑ and pumping technology is selected specifically for the application, which permits a wide range of substrate combinations.
When combined with an external gas accumulator, the Universal Digester offers an excellent, long-lasting tank solution with a digester chamber volume of up to 7,000 m³. The flexible construction method and individual adaptability have been proven over hundreds of projects worldwide.
Central agitation combined with external heating – UniCentralmix
UniCentralmix offers a standard digester solution for industry and communities. The core of the tank is in stainless steel (Verinox) and it is fitted with a central agitator. The central agitator lowers the energy requirement and ensures uniform mixing of the substrate. The smooth internal walls also reduce the build up of deposits in the digester.
The special feature of this tank is the stainless steel diaphragm roof, which has no bolts. The roof construction is flanged tightly onto the edge of the tank with a special profile, needing no bolted plates. This increases safety, reduces leaks and considerably reduces installation costs.
If necessary, heating and insulation can be fitted to the outside of the tank, increasing the energy efficiency and quality of the digester design. Additional advantages include on-site construction and stepless selection of height and diameter, which makes the UniCentralmix the ideal individually tailored container solution for industrial and municipal applications.
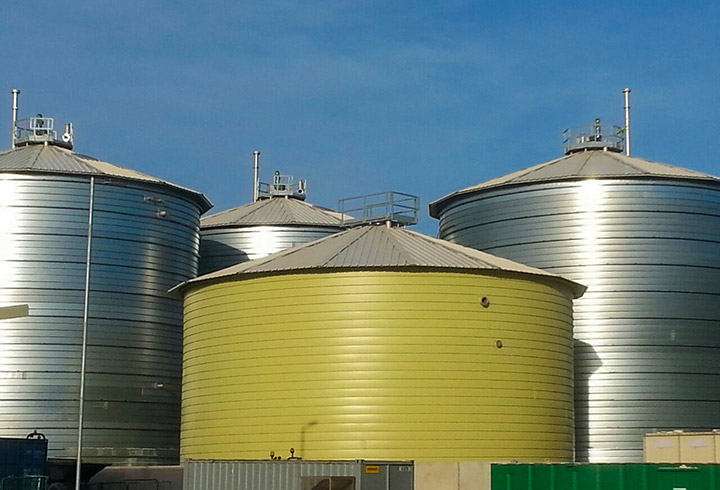
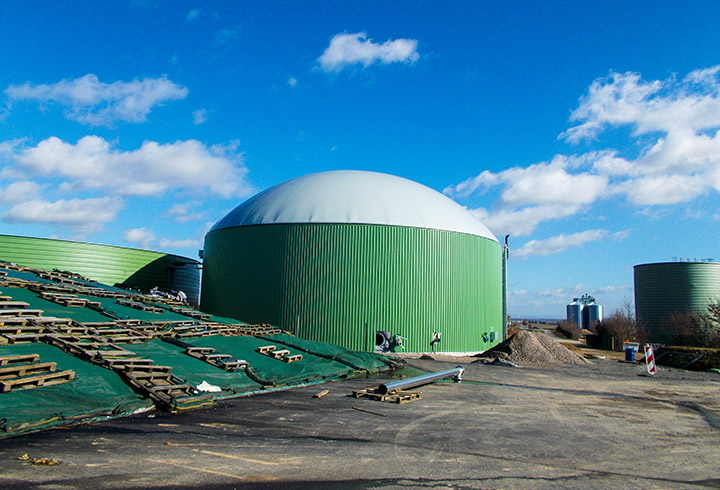
Maximum flexibility with various roof designs and optional accessories – Eco Digester
The Eco Digester has been specially developed for agricultural applications and its flexible construction enables many substrates and applications to be handled. The Digester is available with or without a gas accumulator and with a chamber volume up to 10,000 m³.
Foil roofs, single / dual skin roofs and double diaphragm roofs are also available for this digester as well as high quality stainless steel diaphragm roofs. A wide range of optional accessories is also available. Overall costs are kept low as we assemble the product ourselves.